When updating, expanding or scaling a manufacturing process, it’s amazing how quickly logistics can complicate the project.
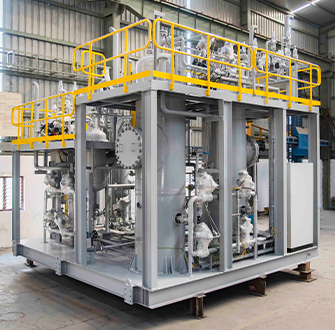
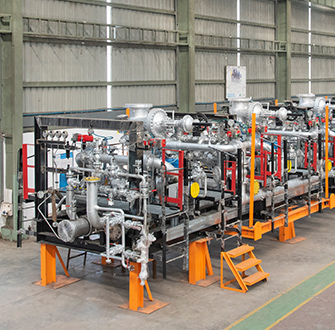
Long lead times on equipment, delays with on-site fabrication, and facilitating communication between vendors have all proven to drive up capital costs and slow time to production.
In recent years, manufacturers have steadily increased their reliance on a faster and less expensive alternative to traditional stick-build process systems. Modular process skids offer a unique mix of flexibility and robustness that traditional stick-build process systems can no longer compete with, especially for the price. By installing modular process skids, manufacturers of pharmaceuticals, food and beverage, consumer products, chemicals, oil and gas can bring their product to market faster, cheaper and with less hassle.
If you work in one of these industries, chances are you’ve heard the term in passing, but exactly what are modular process skids and when should you use one? In this post, we’ll define modular process skids, explain their benefits, and show some examples of process skids that were custom-built for manufacturers.
Shorter Project Timelines – fabricating process skid packages offsite allows on-site facility upgrades to proceed concurrently without interruption. Completing these steps in parallel can eliminate months off the project schedule, allowing manufacturers to bring their product to market faster.
Higher Quality Fabrication – Fabricating skids in a controlled shop environment eliminates weather-related risks and setbacks. It also reduces the need for craftsmen to perform overhead welds. Instead, shop craftsmen use orbital welders to do pre-fabrication on most materials, resulting in more precise welds.
Rollout Savings – Manufacturers needing to install multiple skids across different locations can leverage engineering and design costs from the first skid and fabricate multiple replicas at a reduced cost for each process skid thereafter.